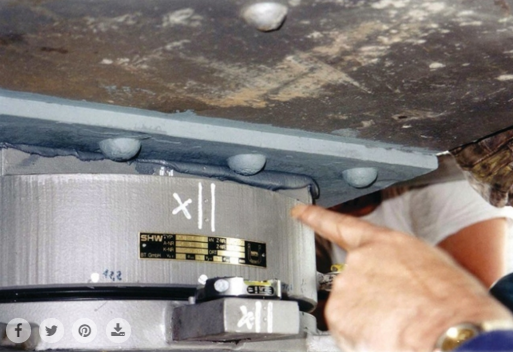
FRANKLIN, Ohio, June 22, 2016 /PRNewswire/ -- America has 609,539 bridges – and now, nearly 1 in 10 of them – 58,495– have been designated as structurally deficient and in need of repair. This, according to US Transportation Department documents. A major part of this problem is maintenance for older bridges: of the 250 most traveled bridges needing repair, 85% of them were commissioned prior to 1970.
Congress authorized a five-year $305 billion highway bill last December, but now the worry is that state DOTs, which provide matching funds, will slow down work on projects unless a more predictable funding source is secured.
Meanwhile, the Transportation Department estimates there's a$115 billion backlog in repairs for US bridges that are structurally deficient or obsolete. (A bridge is rated structurally deficient and in need of repair if its safety rating is four or less, on a scale of zero to nine.)
Private and public sector experts agree the clock is ticking, and that bridge tragedies such as the one in Minneapolis, which killed 13, injured 145, and caused millions in business disruptions, are inevitable unless America gets serious about restoring its bridges to safe and serviceable condition.
Bridge repair is a hot topic this political year, partly because it's entwined with discussions about taxes to fund it: $9.3 billion is needed for bridges in New York alone, $7.5 billion for Pennsylvania,$6.8 billion for California, according to an estimate by the US DOT, Federal Highway Administration, published in 2011. Undoubtedly, costs have moved higher since then.
In the US, that is.
Throughout Europe, bridge repair is done differently. Even bridges older than ours – common in Europe – are restored and maintained at a fraction of what our methods cost.
Highest Bridge Repaired
The Müngsten Bridge is the highest steel rail bridge in Germany. When this 116 year old steel girder bridge underwent a major renovation in 2013, a critical task was replacing the bridge bearings and connecting new bearing plates to the steel structure.
To complete the repair, contractors used a 100% load-bearing gap compensation material that is standard throughout Europe, and has been successfully used in more than 1000 construction applications worldwide. Originally developed for steel and steel composite bridges, it is also used in power plant construction, offshore platform repair and waterway maintenance.
This repair technology uses a polymeric resin with exceptionally high shear strength, and compressive strength. It provides extremely long term corrosion resistance, and is electrically non-conductive. It was engineered specifically for conditions of extreme vibration and temperature, and provides high resistance to weathering, aging, gasoline, oils, coolants, salt and acids. It also cures in 24 hours; as a result, so it allows all repair work to be completed on-site.
The product, MM1018 from Stronghold Coating Systems (Franklin, OH) was used to attach filler plates to the Müngsten bridge base. After gap compensation was complete, the plates formed the bearing surface for the new bridge bearings. The process enabled 100% gap filling without machining – another huge cost advantage.
MM1018 was also used in new construction, for German's Nuttlar Viaduct, 2165 ft. (660 metres) long, 337 ft. (115 metres) high structure that spans the Schlebornbach Valley, in North Rhine Westphalia, the most populous region in Germany. It is scheduled for commissioning this year.
In this case, MM1018 connects the bridge bearings to the steel box girders of the bridge. A 1.96" (5 cm) surface-milled steel plate supports the bearing, and is welded to the underside of the steel superstructure.
The gap between the steel support and superstructure is filled with MM1018. For this reason, the weld has breaks into which the injection and deaeration packer is inserted. This construction has 12 injection and deaeration connections. The injection process saves time and expense, and precludes the need for costly filler plates.
In applications throughout Europe, MM1018 has proved to be a practical alternative to traditional methods for 100% force-fit connections between bearings and construction. It is now sold in North America, exclusively by Stronghold Coating Systems.
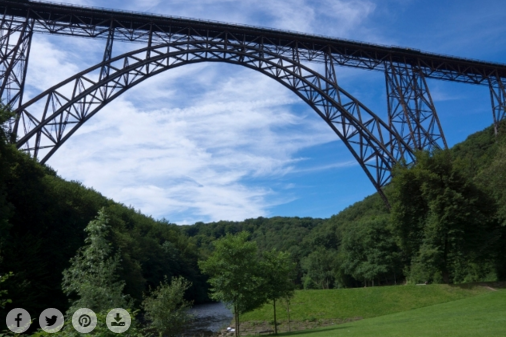
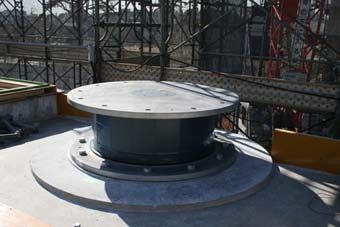